Off-line / in-line supply of eggs or both, the SANOVO GraderPro can be configured to operate with eggs coming directly from the layer houses or from trays and loaded by a SANOVO Optiloader to the SANOVO GraderPro.
Industry-leading, high-end egg grader developed based on 60 years of egg grading experience. Full efficiency, highest food safety standards, maximum hygienic design.
The GraderPro is setting the industry benchmark for efficiency, hygiene, and food safety. This model is able to handle up to 216,000 eggs/hour (600 cases/hour).
Efficiency - By re-designing the main track alongside the new no-side-impact technology, the GraderPro can run with reduced track-speed of up to 25% compared to other manufactures. There is no compromise on capacity and gentle egg handling is significantly increased. All that combined with the smallest footprint possible.
Hygiene - The design of the machine ensures that the all-integrated CIP (cleaning-in-place) cleans all parts without blind spots in a cost-efficient way. No disassembling of parts for cleaning is required, resulting in less downtime, time spent cleaning, and overall lower production cost.
Food Safety - With 100% egg traceability you develop your business alongside increasing food safety requirements by the European Food Laws, USDA, KAT, IKB, Lion Code, and much more. Egg tracking enables you to track your eggs back to where they come from. On top of that our machine parts are food contact material approved, documented in our declaration of compliance.
1. Accumulator
2. Loader
3. UVC disinfection and brush system
4. Leaker & dirt detection systems
5. Crack detection & weighing system
6. Side exits for off-grades
7. Orientator
8. Top and side printing
9. Blood detection & removal gate
10. Packing lines with Traystackers
11. Packing lines with or without closers
12. End release or re-run belt
13. Independent operator system

Leak, dirt, blood, crack and color
A complete program of all the possible detection systems. Proven technology, with a proven track record. Leak, dirt, blood, crack and color detection can be operated to make sure you can provide the best quality eggs to your customers.

Color detection
With color grading, batches can contain both brown and white eggs. The grader will recognize these eggs and will send them separately to a packing lane, so only a specific color is put into a pack. By color detection, a batch of mixed eggs are available on the infeed and only specific colors are on the lanes.
This optional functionality is possible with the dirt detector and assist to get homogenous color output on your final product. Fully automatic the grader will isolate unwanted egg shell colors or even go further create classes with a unified shade of brown eggs into a pack.
Every egg has a tag
From the first detection system in the grader, the software tracks every single egg until packed in the carton.
More exits
SANOVO GraderPro offers a standard of three more exits without the use of packing lanes and thereby no pollution of main track or packing lanes.
Drop-gate for leaker eggs
Next to the side exits for whole egg removals, there is one drop gate for leaker eggs. Those are removed immediately after the dirt & leak detection and dropped into a bin.
Well proven
The very robust and well proven weighing and crack detections will serve you efficiently for many years. Everything is washable and easy to clean – simply activate the CIP on the control panel.
Cleaning in Place
Cleaning in place saves both natural recourses as well as manpower. No plastic destroying UVC light. The SANOVO GraderPro can be CIP in the accumulator, infeed, removal gates, crack detectors, weighing scales, inserter and main track. The packers and packing lanes can be washed down.
Perfectly orientated eggs
Robust and extremely simple design; a design with no moving parts. The system ensures minimum maintenance costs and at the same time ensures your eggs are perfectly orientated.
Flexible printing
The design of the main track makes it possible to print eggs on top or on the side (or both) and thereby eliminating the need for printers on the packing lanes and therefore keeping your investments to a minimum.
Gentle egg transfer
The newly developed inserter system places the eggs point down and at the same time synchronizes the speed to the main track. This is done in such a way to avoid damaging or stressing the eggs. This ensures an extremely gentle transfer, where your eggs are treated as gently as possible.
Efficient
Placed at the beginning of the main track, it is very accessible and easy to clean. With zero measurement for each egg to compensate for outside light and the individual color of the egg.
Easy operating
The user-friendly control system, enables you to control the complete grader.
Reduced by up to 25%
Very gentle handling of the eggs through an increase of the egg carrier transport density. The main track transport speed can be lowered to move the same amount of eggs, thus we achieve:
- slower transfer speeds;
- more gentle egg handling;
- higher yield on your investment
Small footprint
With little footprint and adjusts to every pack individually. High operation reliability even with poor packaging.
Are you looking for sustainable packaging? Tap into Hartmann and experience their packaging options that will help you increase performance.
No side impact
All eggs are treated very carefully and throughout the whole machine, they are delivered downwards and with no side impact, thus ensuring a higher yield.
High capacity
The packers have a buffer capacity of 78/114 eggs each (GraderPro 400/600), which eliminates operational stops of the packing lanes.
Overview
For each lane you are able to see all necessary information needed, such as: egg sort class, type of packing, egg level in packing, and total number of eggs packed.
Continuous operation with end-release
The end release of the machine frame makes it possible to run the grader on full speed even if the packing lanes are filled up. A possibility is to connect the end release to a breaker system.
Optimize facility
The SANOVO GraderPro has a small footprint along with the highest capacity ever seen in the market, this makes the GraderPro the most efficient grader in the world.
The SANOVO Pack Labeler ensures reliable egg pack labeling, enhancing traceability with information like laying date, grade, and origin. It helps prevent mislabeling, reducing recall risks. This all-in-one solution minimizes equipment suppliers making SANOVO a one stop grading shop.

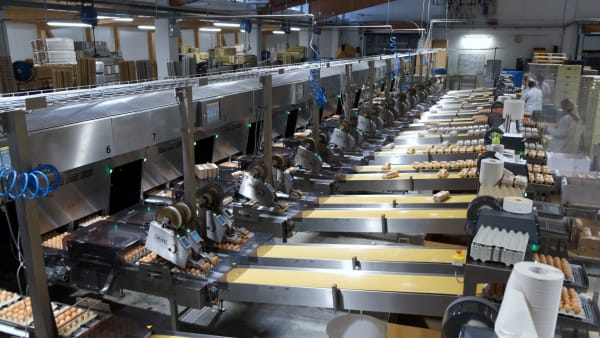
The success story of Gnaser FrischEi and EiVita starts with the foundation of Gnaser FrischEi in 1970 and the goal to produce cage eggs with a flock of around 25.000 laying hens. Read more...
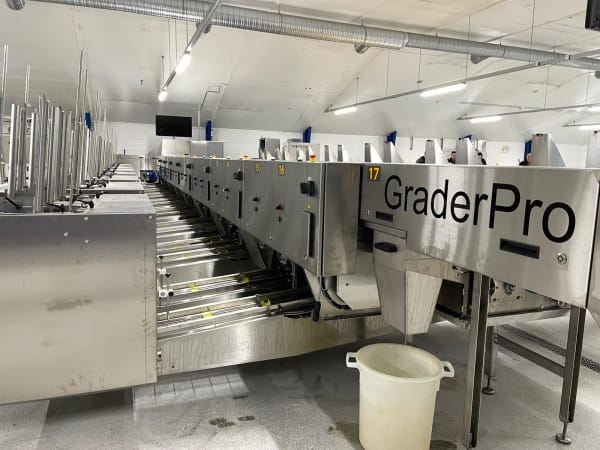
Read about Dava Foods' experience with the SANOVO GraderPro.

Read about how Valley Park Farm invested in grading technology to tackle the labor market challenges associated with farms in Australia.
GraderPro 400
Up to 144,000 eggs/hour
Up to 400 cases/hour
Industry-leading, high-end egg grader developed based on 60 years of egg grading experience. Full efficiency, highest food safety standards, maximum hygienic design.
GraderPro 800
Up to 288,000 eggs/hour
Up to 800 cases/hour
Highest capacity in the market. Industry-leading, high-end egg grader developed based on 60 years of egg grading experience. Full efficiency, highest food safety standards, maximum hygienic design.
Egg Palletizer
Up to 144,000 eggs/hour
Up to 400 cases/hour
An anthropomorphic, robotic egg case palletizer, able to palletize at a speed of 400 cases/hour (144,000 eggs/hour)
De-Palletizer 600
Up to 216,000 eggs/hour
Up to 600 cases/hour
The De-palletizer machine gently handles plastic trays at a capacity of up to 600 cases/hour (216,000 eggs/hour). Can also handle interlayers and pallets
Case Palletizer
Up to 216,000 eggs/hour
Up to 600 cases/hour
Anthropomorphic, case palletizing robot able to palletize at a speed of 600 cases/hour (216,000 eggs/hour)
Case Packer Twin
Up to 57,600 eggs/hour
Up to 160 cases/hour
Case packing solution designed for all kinds of egg pack sizes and cartons. Largest variety of pattern combinations, high capacity, modular design.
Tray Washer - Off-line STW-2/3
STW-2: up to 6,500 trays/hour
STW-3: up to 10,000 trays/hour
Automated tray loading, washing, and conveying unit available in two or three-line tray infeed for destacking. This tray washing machine is optimized for off-line operation. Efficient, compact and labour-saving design.
Tray Washer - In-line STW-12/18
STW-12: up to 5,000 trays/hour
STW-18: up to 7,200 trays/hour
Automated tray loading, washing, and conveying unit available in two or three-line tray infeed for destacking. This tray washer model is optimized for in-line operation with the OptiLoader Plus 12 and 18. Efficient, compact and labour-saving design.